
The ring of the hammer on an anvil was once a familiar sound in every country village, where the Blacksmith was a vital part of the
community, and, in the census of 1841, Witheridge had four blacksmiths shown as serving the local community. They would have had an
important role in making and mending most of the machinery for local farms and the household, and in repairing all sorts of tools and
implements brought to them by the farmer. In many cases, the iron and steel implements used on the farm were probably also made in the
smithy.
"He'd do repairs to plough's, disks, and harrows. Farmers would bring up to the shed 3 or 4 spades at a time, to have
the handles repaired.
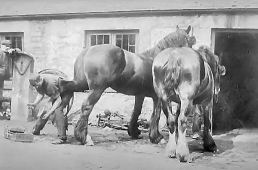
Many Blacksmiths were also farriers, and, with the horse being the main means of power, there were large numbers of horses at work in
the countryside and needing shoeing, and this kept the blacksmith busy. Clothed in a leather apron, and working the fire with hand-operated
air bellows, the blacksmith would place the metal into the roaring fire to get it hot. On reaching the correct temperature, he would
transfer the hot metal from the fire on his long tongs to his anvil, where, with his hammer, he would skilfully knock it into the shape
of a horseshoe. Then, after dipping the hot metal into cooling trough at the front of the hearth, he would then go to where the horse
stood patiently waiting. Then, with his back to the horse, he would pick up the horse's foot, and holding it between his legs, he would
remove the old shoe. After cleaning the foot, he would pare the hoof using a rasp, searcher and pairing knife. He would then offer the
new shoe up to the foot, and, once satisfied that the new shoe fitted perfectly, he would nail it in place.
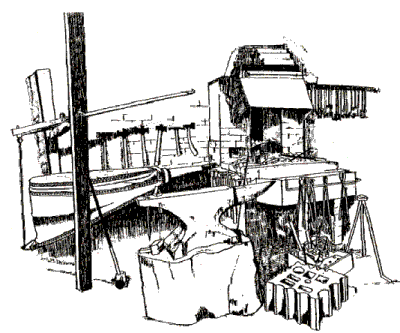
The forge or smithy was not only the place where the important farm horses were shoed, but also the place where the Blacksmith would
manufacture tools and equipment for use on the farms. He worked long and hard hours, usually for very little pay, and it was quite
common to receive payment in kind, but at the time of the 1841 census, records show some 112,000 Blacksmiths worked in the Country. Little
over a century later though, this figure was in sharp decline as the use of motor tractors and cars increased at the expense of horse
drawn vehicles. His was a craft that was often a family tradition, with the skills passing from father to son. Occasionally he might
take on an apprentice, who started by paying his master a small weekly fee, gradually receiving a small wage himself as he became more
skilled.
Little over a century later though, this figure was in sharp decline as the use of motor tractors and cars increased at the expense
of horse drawn vehicles. Blacksmiths work by heating pieces of metal (usually steel or iron) with a forge, until the metal becomes
malleable enough to be shaped to a desired outcome via repeated manipulation with a hammer, punch or other tooling against an anvil.
It would have begun back in the Iron Age when early man first began to make tools from iron. It would have started with a simple
observation that a certain type of rock, when heated by the coals of a very hot campfire, yielded a metal called "iron". We can say
therefore, that the art of blacksmithing, turning that crude metal slag into a useable implement, has been around for thousands of years.
And beyond making those first simple tools, the first spear or arrow tips, the first cooking spit, the craft would require hundreds more
years before mankind realized the magnetic properties of the forged metal. The first compass used a forged iron needle that floated in
a round vial. This was a great discovery. By forging the needle as perfectly as he could, the blacksmith aligned the molecules in the
iron and that is why north is north and south is south. From that point on, sailors could travel without need of stars or sun to plot
their courses around the globe.
As to where and when blacksmithing evolved depended on supplies of fuel and iron ore. Charcoal was the primary fuel in many places. Coal
needed converting to coke, a fuel that generated even more heat than charcoal. Iron ore, early man discovered, was present in rock
strata that had a red colour and the deeper the red hue, the higher the iron content. Then it became a quest to find the rock strata
that gave up its iron with the least amount of work. Given the weight of the ore rock and the large amounts of fuel needed to smelt the
ore, the earliest ironworks were located in areas where both ingredients were ample and in proximity to each other.
Early iron smelters consisted of an oven built from rocks that could withstand repeated heating. These ovens looked like beehives with
a smoke vent in the top and an entry portal on the side. The hearth containing charcoal or coke, set afire, and the ore rocks placed on
top. When the temperature rose above 2000 degrees, the iron would flow from the ore and 'puddle' in the fiery coals.
With large tongs, these lumps of raw iron would be pulled from the oven, and placed on an anvil. A man would then hammer the lumpy piece
of raw iron into a flat, rectangular bar. The bar would be folded over and hammered again to its original shape. This process would
continue several more times until all impurities had been driven from the ingot. The finished ingot, bearing the layers of the folding
process, was called "wrought iron".